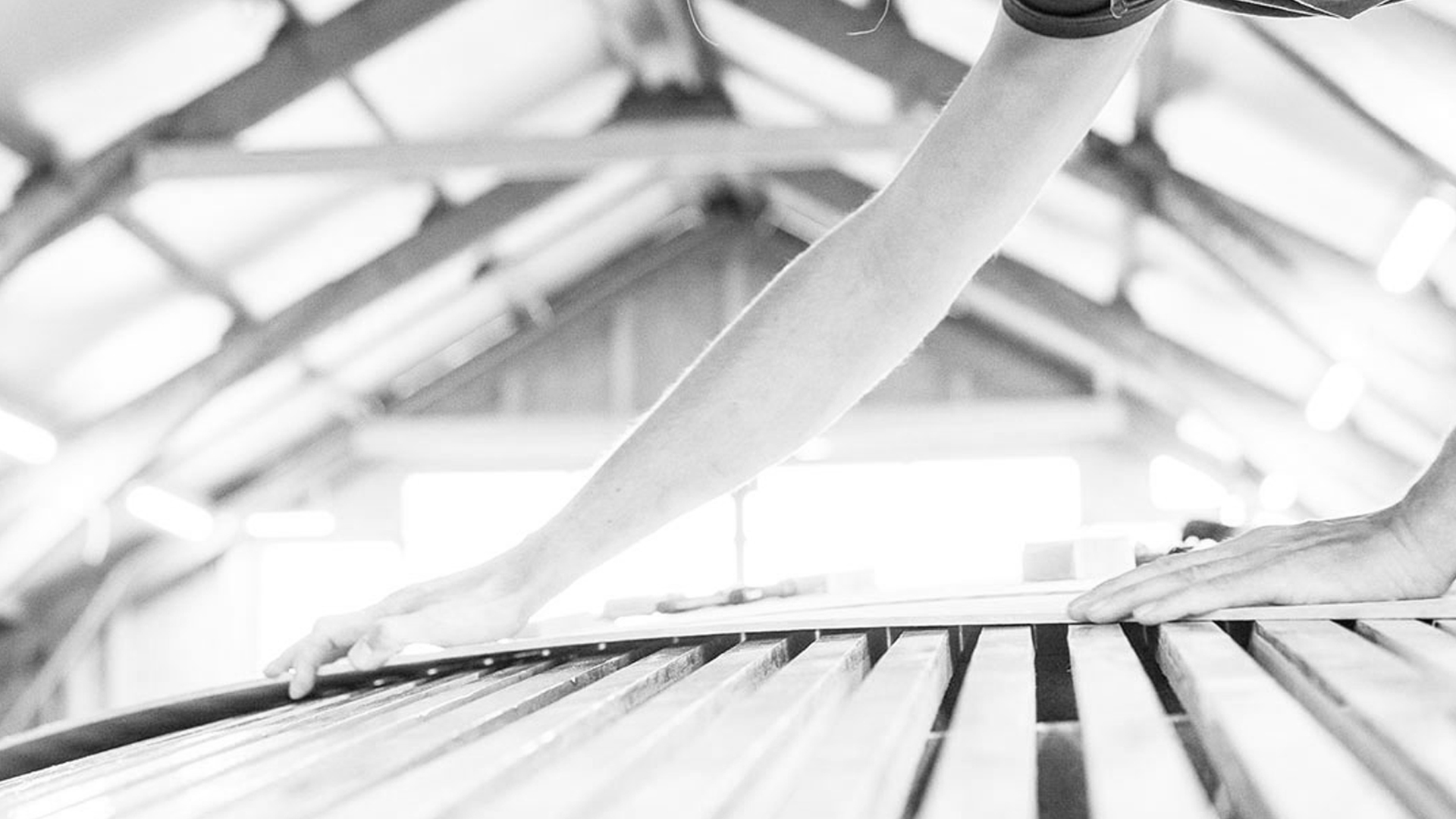
EXOSKIN
OUR METHOD OF BUILDING YACHTS WITH WOOD
The method we offer is an advanced wood construction. It allows us to build boats of all sizes, which are stiff, lightweight, and contribute to the reduction of CO2 emissions.
All details add up to a 20% increase in strength to weight ratio.
For the construction of our 15 meter design Elida, we decided to continue the development of modern wood boat building techniques, using the latest developments in wood science, in order to bring this material to modern standards.
The construction method is certified by DNVGL including for the toughest sailing conditions of offshore racing.
As time moves on and we all re-discover the possibilities of this noble material outside of pure racing, consider this for your next project.
Discover more about this exciting new method below.
EXCELLENCE AND PRECISION
4 LAYERS OF WOOD, AND AN OPTIMIZED COMPOSITE EXOSKIN
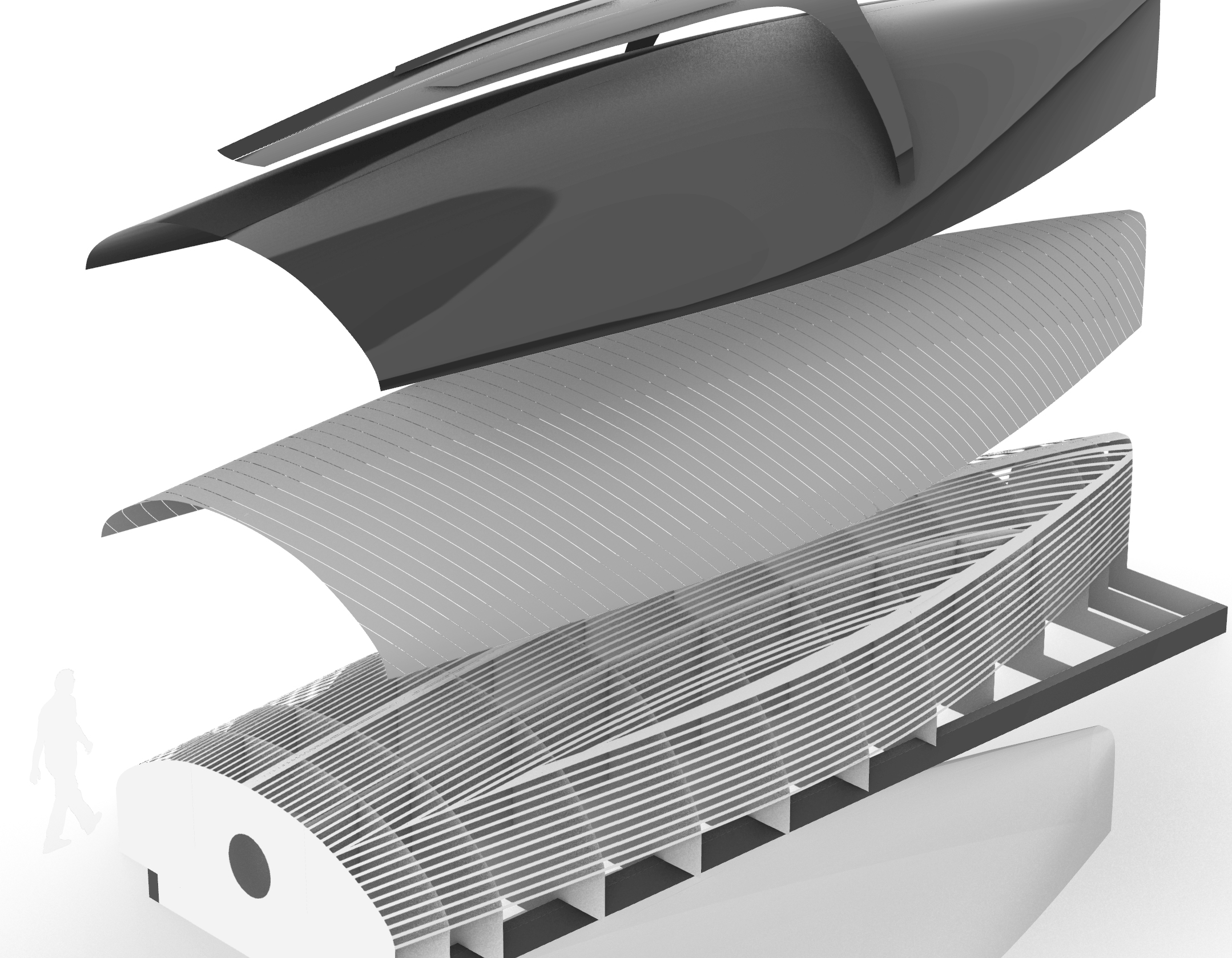
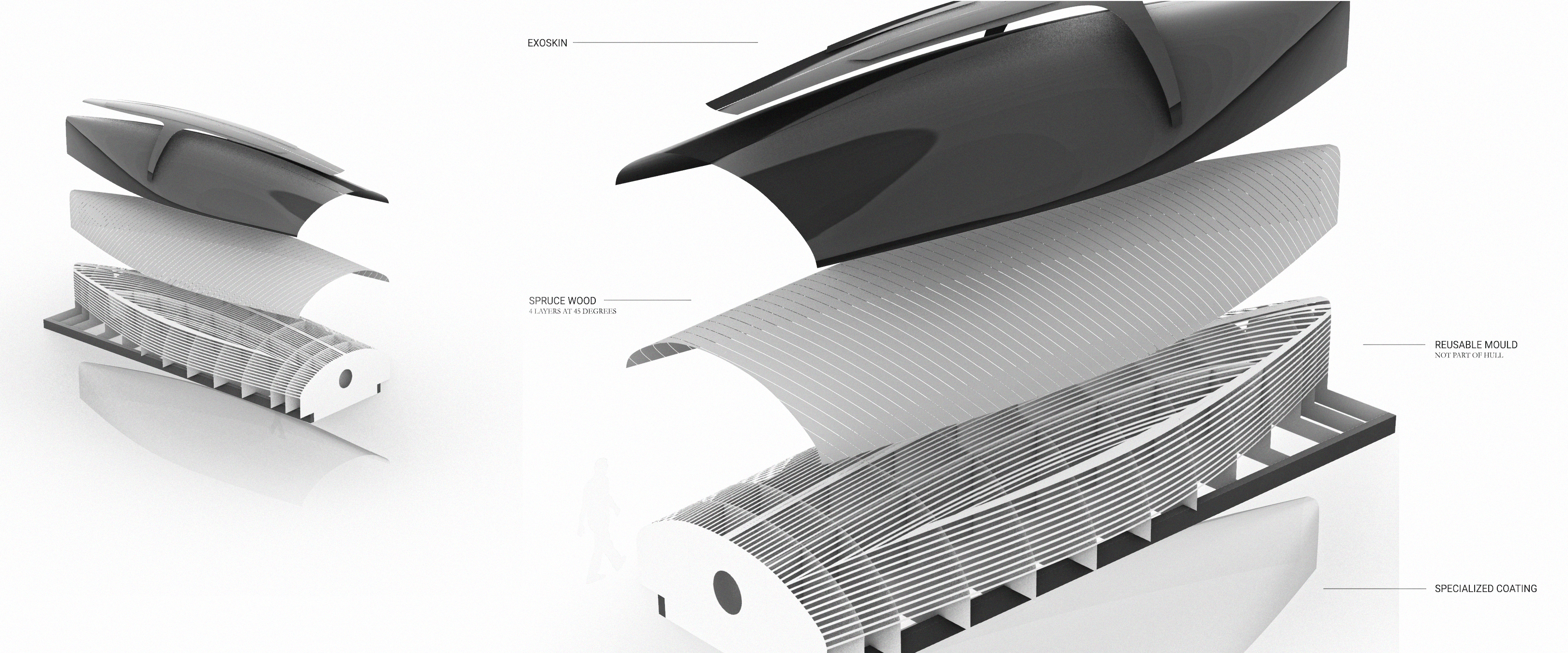
THE CONSTRUCTION IN 4 KEY POINTS:
Our method has more to do with high end composite manufacturing.
1/ 4 layers of wood glued together with our specific epoxy based structural adhesive
2/ precise specification of wood layers and vaccum bagging for an even and reliable bond between layers
3/ wood is sealed from air all around with an outer carbon fibre layer for extra protection
4/ our Exoskin itself is laminated comprising of global composite reinforcements calculated to meet modern standards of stiffness and strength
In addition, the hull is faired by sanding, thus using no fairing paste and saving weight for an additional level of refinement.
‘Exoskin is a modern wood cosntruction method. It takes a little more time, but the result is worth the effort’
Material testing at Airbus facility
SUPERIOR MATERIALS
FOR SUPERIOR PERFORMANCE
THE WOOD CORE
You may be familiar with the term Wood Epoxy from the 1980s. In the last 40 years, developments in wood construction has evolved, and we have now defined a selection process which allows to reduce the variability of the wood we use.
This has resulted in a 20% gain in material properties for the same weight.
Selected local agents, take specific measurements and only keep wood which is in our exact specifications, in a narrow band of density. It is further controlled during the construction at our construction site in Villefranche-sur-mer.
We have selected Northern Spruce as our wood of choice: a type of pine which grows primarily in northern Europe and Alaska. A light wood makes for a thick hull which benefits from additional local stiffness.
‘working with wood mills and certification companies, we select wood within a specific narrow band of density so its properties can be better predicted, for more performance’
Key facts:
– Bare hull weight 620kg in Exoskin vs 510 kg for carbon fibre vs 570kg for Eglass
– Certified by DNVGL for offshore racing Category A
– Construction using Northern Spruce and optimized epoxy based adhesive
– Exoskin is a composite reinforcement optimized with a technology borrowed from Formula One and the America’s Cup